Tokyo / Honda has an ambitious goal, and that’s to be carbon-neutral by 2050. Not just for its products, but also all corporate activities. It is an ambitious goal given the company does not sell a fully-electric vehicle in North America at this time. This will change in the coming years, and it will be accompanied by a number of other innovative ideas.
As it stands, Honda is going to launch its first full-electric ride, a joint venture with GM, in 2024. The Prologue rides on a shared platform and will use a version of the Ultium battery found in the Blazer EV. The joint venture will also go on to develop an “affordable” EV concept. Honda’s CEO, Toshihiro Mibe, said the goal is to develop an EV that will sell for less than US$30,000, and it will be available as early as 2027. This, he believes, is crucial if the mass-adoption of electric vehicles is going to reach the levels the industry and world governments are hoping to achieve — in Canada, this means all new light-duty cars and passenger trucks will be zero-emission by 2035.
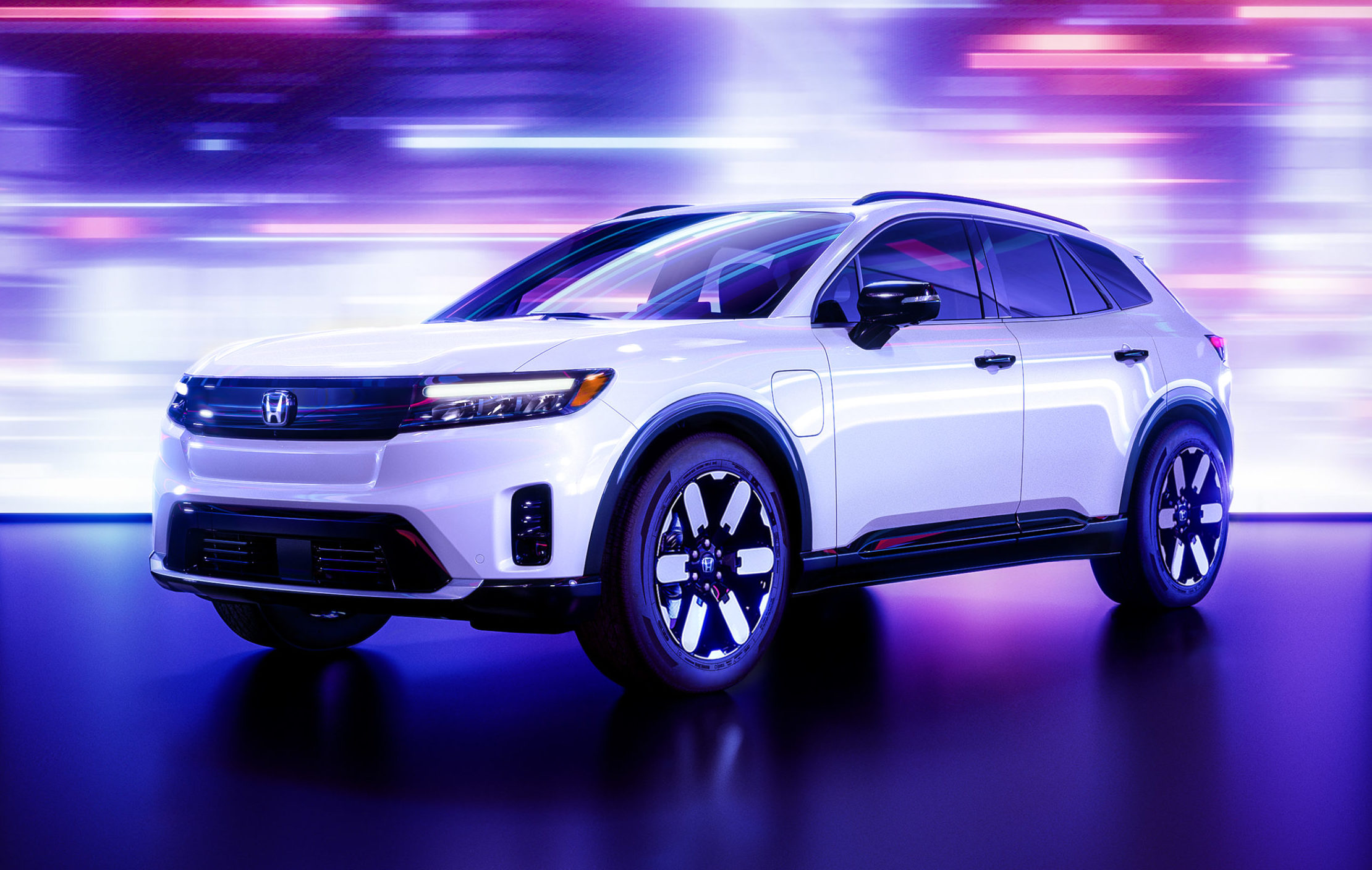
2024 Honda Prologue
The most intriguing and potentially beneficial part of the program is Honda’s planned shift away from lithium-ion batteries and towards a new all-solid-state battery pack the company is actively developing. Beyond the EV and fuel-cell joint ventures it has with GM, Honda is working on its own EV platform and an exciting new battery.
At this point, everyone visiting the battery lab has to wear a lint-free jumpsuit, hair net and rubber gloves. Before entering the lab, the visitor goes through an airlock where they were greeted with a blast of air to ensure they are totally dust-free. Even the soles of their shoes are treated to several tack-pads to clean off any dirt. Cleanliness is key, as contaminates cause headaches!
Read more: Honda invests heavily in US electric vehicle production
In the working lab, various work stations take care of the elements that go into the all-solid-state battery. The cell shown consisted of the two copper/lithium metal anodes that bracket two layers of the solid-state electrolyte with the cathode sitting in the middle. The cathode uses a special slurry that’s applied to an aluminum foil strip.
Once assembled, this elaborate sandwich has the connection tabs added and the whole lot is precision rolled to ensure consistent connectivity (interface adhesion, in Honda speak) over the entire surface of the assembly. The finished pack is then sealed in a plastic pouch to protect it from moisture. At this point, each of the oblong cells being produced is rated at 0.8 kilowatts.
While the process seems relatively straightforward, it is demanding and, at this point, agonizingly slow. The key to mass production is to maintain the lab-like environment and precision of the build process, but to ramp everything up to a real-world speed capable of producing the number of batteries needed. To move beyond the lab-based production, Honda is set to invest approximately $400 million (43 billion yen) to build a demonstration production line for its all-solid-state battery. The goal is to start the demonstration line in the spring of 2024.
The shift to the all-solid-state battery is being touted as a game changer. The current lithium-ion batteries use a liquid electrolyte, which must be sealed to prevent leakage and must include a separator to prevent a possible short circuit between the anode and cathode. These batteries are also more susceptible to the deterioration caused by the heat created by repeated charge/discharge cycle. In contrast, solid electrolytes are more stable, there is no risk of leakage, there’s no need for a separator and they are less prone to the degradation caused by heat.
Of course, the fact the solid-state battery tends to be lighter and has a higher power density than a lithium-ion battery means it delivers a better driving range. Honda says the potential is 1.5 to two times more driving range from a lighter battery that costs less to produce — talk about win/win/win! The solid-state battery also promises better dynamic performance and a shorter charge time because it’s less susceptible to heat. This means an 80 per cent charge can be pumped into an all-solid-state battery in 15 minutes, which is half (or more) the time required by the best of the current batch of lithium-ion batteries.
Perhaps the biggest upside is life expectancy. Where a lithium-ion battery typically begins to degrade after 1,000-1,500 cycles, a solid-state battery has the potential to maintain 90 per cent of its capacity after 5,000 cycles.
Honda has a number of other clever technologies up its corporate sleeve, beyond cars. The first is a wall of switchable batteries that will work across a range of its product. The commercial battery bank holds 12 batteries; the home version holds four packs. The idea is when your electric scooter needs a power-boost rather than stopping and recharging the two 48-volt batteries, the rider simply goes to the battery bank and replaces the two depleted units with charged ones.
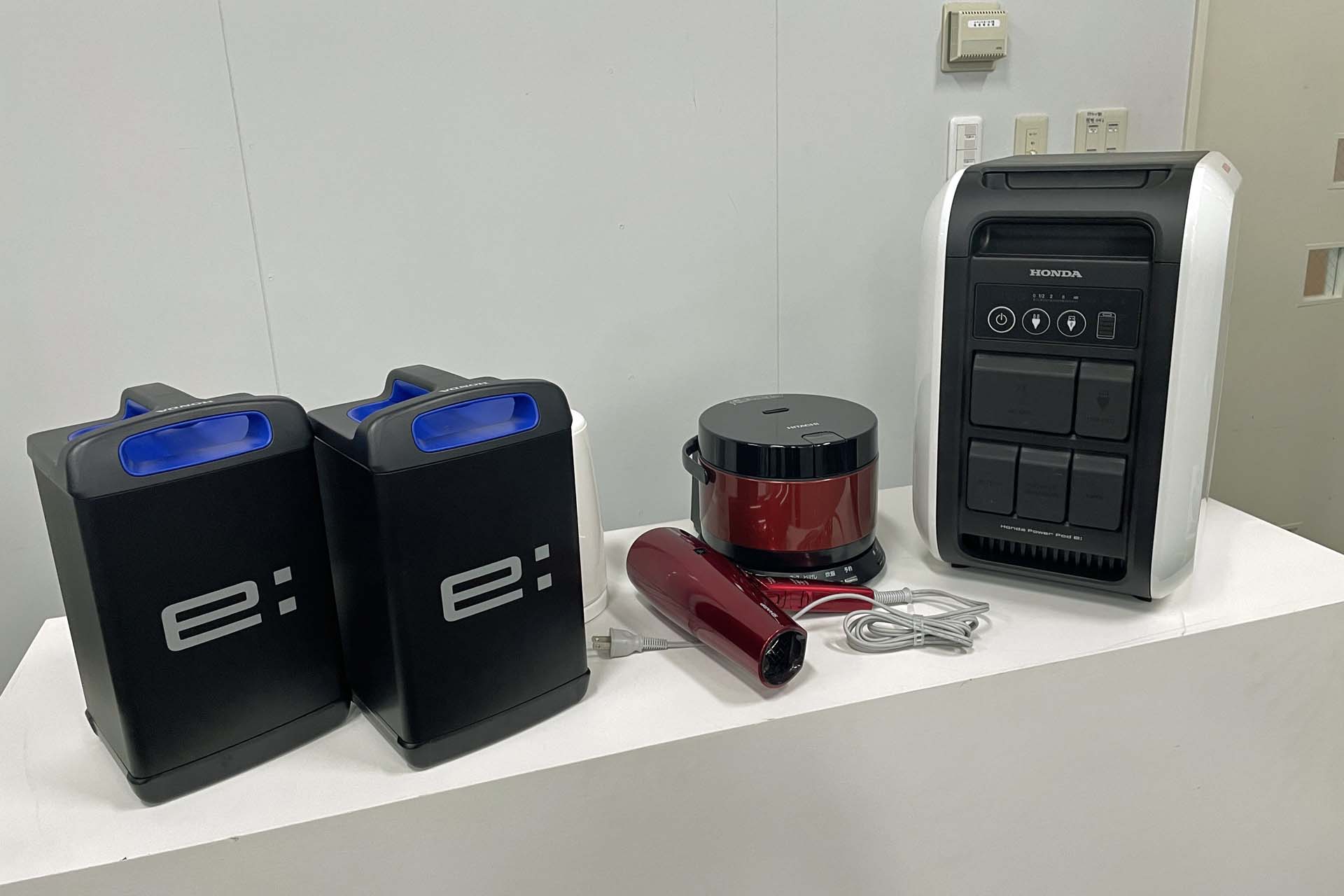
Honda swappable batteries / Graeme Fletcher, The Charge
The swap takes less than a minute to accomplish, which sure beats the thumb-twiddling time it takes to recharge a fixed battery. The unspoken benefit of the design is when the scooter is parked in the garage for winter, the battery packs fit into an all-electric snowblower. Beyond this switch in use, the batteries will also fit into a portable “generator,” an all-electric outboard motor and so the possibilities go.
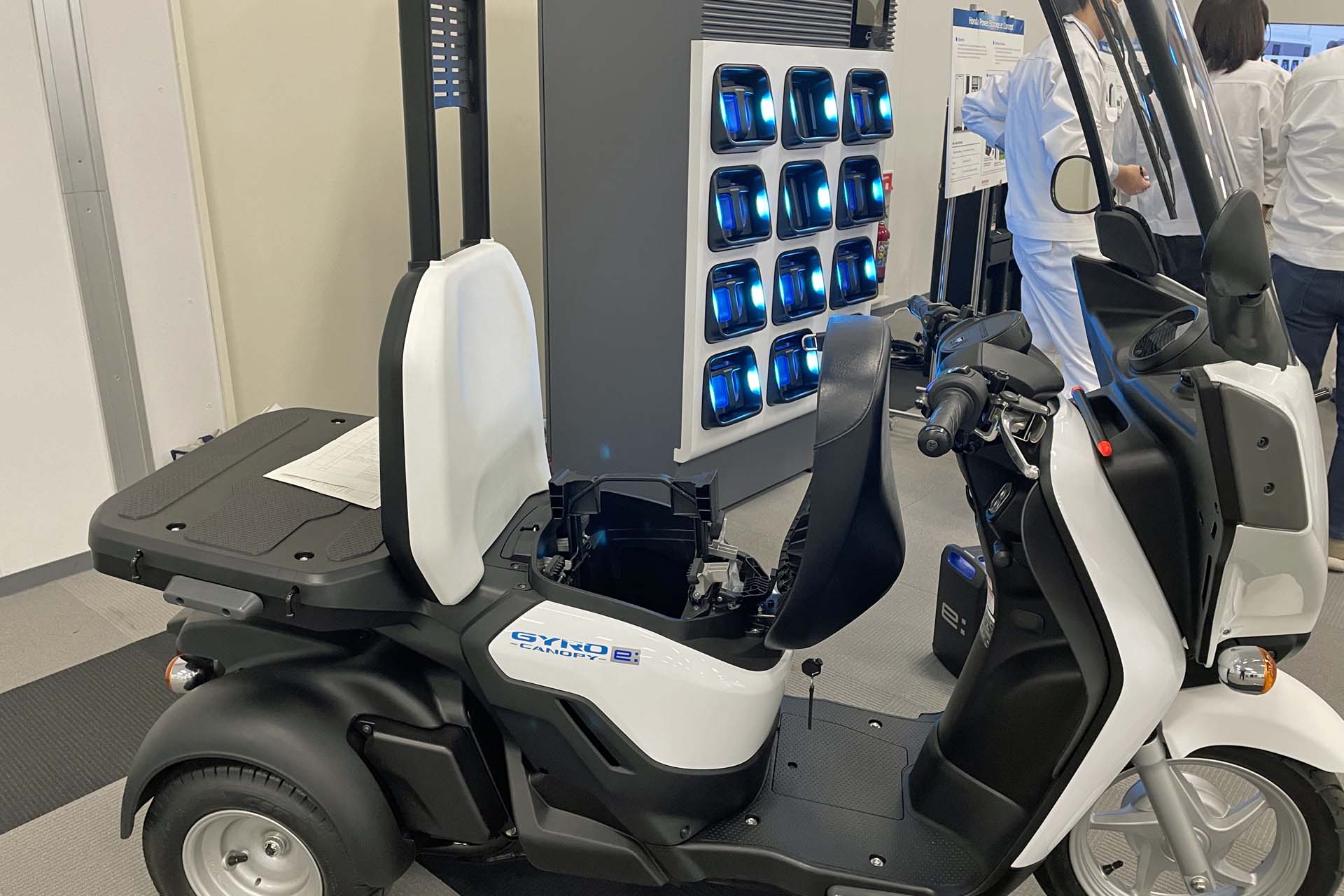
Honda swappable batteries / Graeme Fletcher, The Charge
Another clever move is an alga that actively eats carbon-dioxide — one gram of Honda’s Dreamo alga consumes two grams of CO2. The beauty is the Honda-bred alga allows the ratio of starch-to-protein to be varied depending upon the end use. The process needs sunlight, water, nitrogen and phosphorus for food.
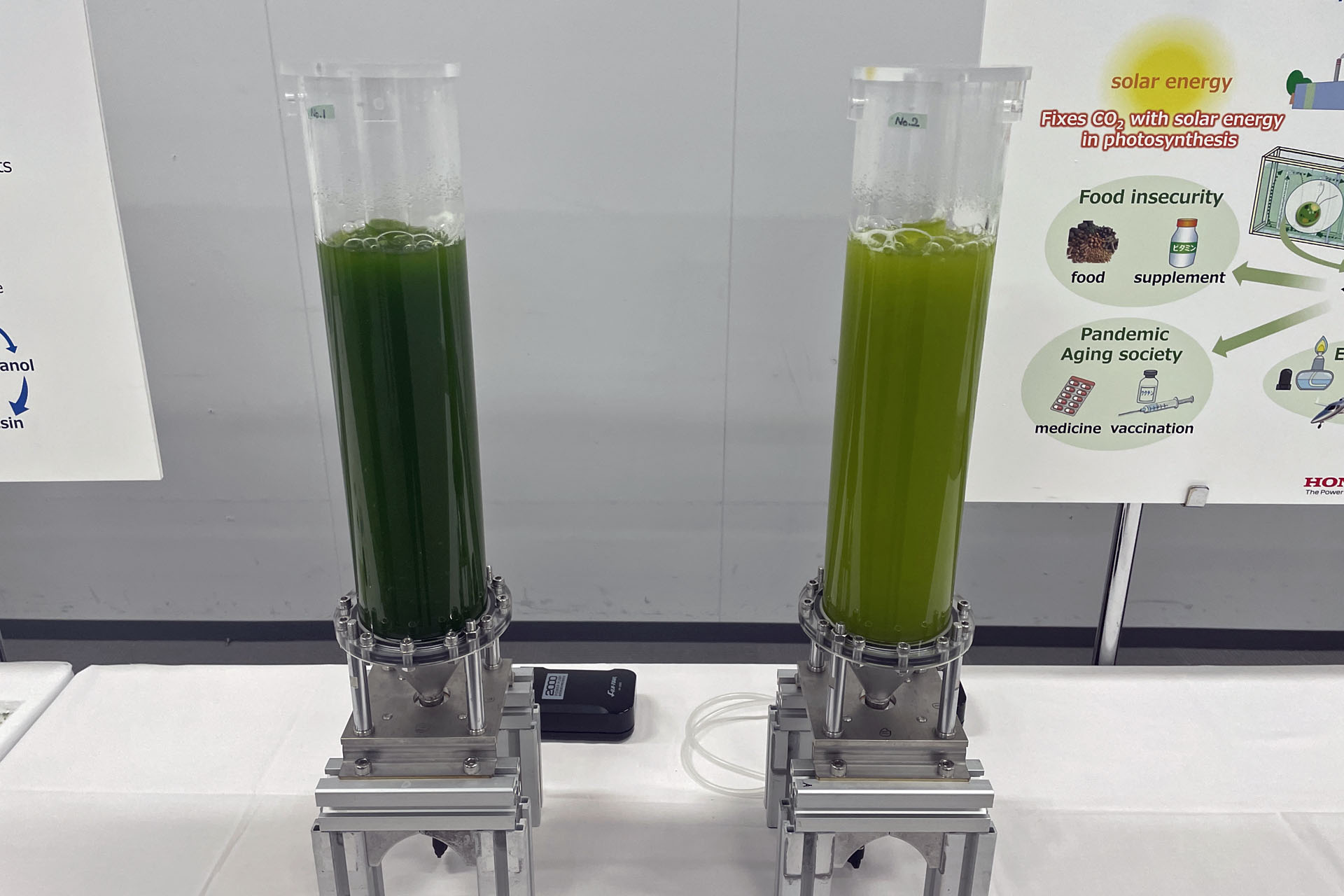
Honda algae
Now, the alga grows to produce protein and carbohydrates while absorbing CO2. The end product can be used as a meat substitute that’s 69 per cent protein. Let the process continue for another three days and the increased carbohydrate content allows it to be used to make plastic substitutes or as a bio-fuel for the Honda Jet. It’s a somewhat unnerving thought a single product can be food or the fuel needed to cultivate it.
Of the technologies shown at the conference, the one that will not likely see the light of day is a closed-circuit fuel cell setup. The closed-circuit approach means the fuel cell uses oxygen and hydrogen stored in high-pressure tanks to produce electricity and water. The electricity delivers the demanded power while the water by-product is collected and returned to a storage tank before being split into the oxygen and hydrogen gases used to feed the fuel cell, and so the cycle goes.
The closed-circuit operation, says Honda, means the process is approaching “100 per cent efficient.” Well, according to the U.S. Department of Energy, hydrogen fuel cells are generally between 40 and 60 per cent energy efficient. Yes, the stated efficiency is for a unit that discards the otherwise waste water, but almost doubling the efficiency by saving and reusing the water remains well shy of the theoretical potential Honda suggests.